Case Study:
Revolutionizing Ophthalmic Packaging for Efficiency and Safety
Reducing Time, Waste, and Injuries: How MPS Pharma Optimized Packaging for a Growing Eye Drop Business.
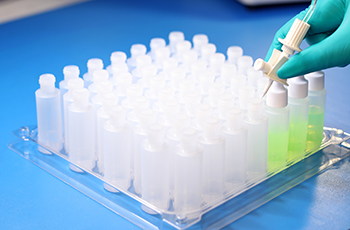
Client Overview
A compounding pharmacy experiencing significant growth in their eye drop business faced operational challenges related to packaging inefficiencies. Their highly skilled staff, dedicated to sterile compounding, were hindered by labor-intensive packaging processes, workplace injuries, and excessive waste.
The Challenge
Scaling up their eye drop production exposed inefficiencies in their existing bottle packaging system:
- Labor Inefficiencies: Pharmacy technicians and pharmacists spent excessive time opening thousands of individual two-pack packages, diverting attention from compounding tasks.
- Workplace Injuries: Repeated packaging handling caused minor but persistent injuries, such as blistered fingers and repetitive strain aches, impacting team morale.
- Waste Management: The excessive packaging created substantial waste, complicating disposal and increasing costs.
- Particle Control: Each package required wiping for particle control before being transferred into sterile environments, further consuming time and resources.
The pharmacy needed a streamlined packaging solution to support their growth without compromising sterility or compliance.
The Collaboration
MPS Pharma collaborated with the pharmacy’s sterile fill team to thoroughly analyze their workflow and packaging challenges. Together, we identified key inefficiencies and co-developed a tailored solution to address their needs.
The Solution
Leveraging MPS Pharma’s existing ophthalmic line, a custom packaging solution was designed to improve efficiency, safety, and waste management.
Key features of the solution:
- Triple-Layered Packaging: Reduced the need for individual wipe-downs during transitions between the warehouse, material pass-through, and compounding areas, streamlining the process.
- Increased Packaging Efficiency: Consolidated the number of bottles, tips, and caps per package, dramatically reducing the number of packages handled.
- Example: For a batch requiring 10,000 caps, the number of packages opened dropped from 5,000 to just 50.
- Compact Design: Reduced packaging volume, saving storage space and cutting monthly shipping costs.
The new system was fully validated to meet sterility and particle control standards while significantly enhancing operational efficiency.
Implementation Process
Prototypes were rigorously tested in collaboration with the sterile fill team to ensure compatibility with existing workflows. MPS provided ongoing support during rollout, including training and documentation to ensure seamless adoption.
The Results
- Significant Time Savings: Reduced the number of packages opened by up to 100x, allowing technicians to focus on compounding tasks.
- Improved Workplace Safety: Eliminated repetitive injuries caused by frequent package handling, boosting team morale.
- Reduced Waste: Streamlined packaging minimized waste, simplifying disposal and reducing environmental impact.
- Lower Shipping Costs: Efficient packaging design reduced shipping volume and saved on transportation costs.
Facing challenges with packaging inefficiencies? Let MPS Pharma help you design solutions tailored to your unique needs. Explore our Collaborative Innovations today.
Have any questions?
Contact our Customer Service team for additional support at
(844) 641-3814 or by email at sales@mpspharma-inc.com