Case Study:
Enhancing Aseptic Handling with the TipGuard Ophthalmic Bottle Cap
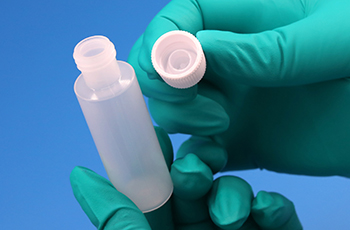
Client Overview
A growing compounding pharmacy transitioning from 503A to 503B operations faced increasing production demands and more stringent FDA compliance requirements. Known for their commitment to quality, they needed a solution to streamline workflows while maintaining aseptic integrity.
The Challenge
Scaling up operations brought several challenges, particularly with the manual handling of a traditional three-piece bottle system, consisting of separate bottle tips and caps. Leadership identified two critical issues:
- Labor Efficiency: The growing volume of compounded medications increased the time and effort required to manually place bottle tips using tweezers.
- Aseptic Handling: Handling the drop tip raised concerns about maintaining aseptic standards critical to meeting FDA compliance.
The pharmacy needed an innovative solution to optimize their workflow while ensuring the safety and integrity of their products.
The Collaboration
MPS Pharma partnered with the pharmacy’s leadership team to thoroughly understand their workflow, pinpoint inefficiencies, and address compliance concerns. Through a collaborative process, we designed a tailored solution that integrated seamlessly into their operations.
The Solution
MPS Pharma developed the TipGuard Ophthalmic Bottle Cap, an innovative cap with an embedded tip. This solution eliminated the need for manual tweezer placement and reduced direct handling of critical components, addressing both labor and aseptic handling challenges.
Key features of the TipGuard design:
- Embedded Tip Inside the Cap: Simplifies assembly by eliminating direct contact with the tip.
- Streamlined Workflow: Reduces the number of handling steps, improving efficiency and safety.
- Multiple Colors & Works with Multiple Bottle Sizes: Enables reduced inventory needs and enables differentiation of drugs.
MPS Pharma oversaw the design, manufacturing, sterilization, and full validation of the TipGuard product, ensuring a turnkey solution for the client.
Implementation Process
Prototypes were quickly 3D printed and tested in collaboration with the pharmacy’s team to ensure usability and compatibility with their equipment. MPS Pharma provided detailed instructions and training to ensure a smooth transition to the new system.
The Results
- Improved Labor Efficiency: The pharmacy reduced handling steps, saving significant time and labor costs as production scaled.
- Enhanced Aseptic Handling: Eliminated direct contact with the tip, minimizing contamination risks and ensuring FDA compliance.
- Scalable Operations: The streamlined process supported the pharmacy’s transition to 503B operations, positioning them for continued growth.
Facing challenges in your pharmacy operations? Let’s collaborate to design a solution that meets your unique needs. Discover how MPS Pharma’s Collaborative Innovations can help streamline your workflows.
Have any questions?
Contact our Customer Service team for additional support at
(844) 641-3814 or by email at sales@mpspharma-inc.com